[Analytics] How to build agile, resilient supply chains against global disruptions
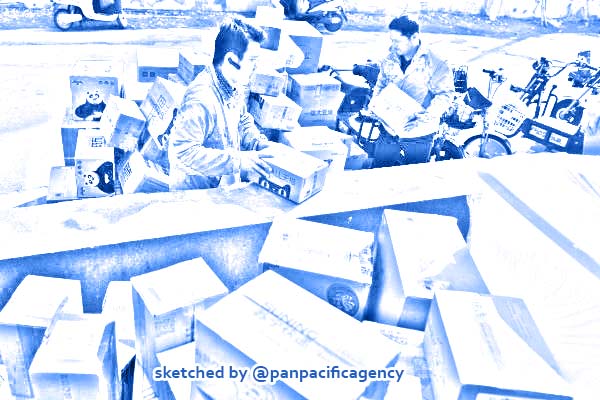
Workers of Chinese e-commerce retailer Suning Group sort out parcels at a distribution center of Suning in Nanjing city, east China's Jiangsu province, 13 November 2018. Sketched by the Pan Pacific Agency.
Despite its severity, the COVID-19 pandemic is but one of many shocks that lead to multiple demand and supply stressors affecting supply chains worldwide. Given the recurrent and diverse risks of such disruptions, an immediate response alone is not enough to ensure long-term supply chain resilience. Kuntha Chelvanathan specially for The Business Times.
The pandemic has interrupted the flow of goods with the suspension of container services, freight reroutes and “blank sailings”, where global shipping companies are ordering vessels to skip entire strings of ports. This has led to an increase in transportation and storage costs and the risk of failure to fulfill contractual obligations.
Due to the multi-tiered nature of global supply chains today, manufacturers in Southeast Asia are discovering that even if direct suppliers still operate, the suppliers of their suppliers may be affected. Even though Southeast Asia is a key manufacturing hub, it is still largely dependent on China for intermediary products. For example, many critical components in smartphones are manufactured in China before they are shipped for assembly in Southeast Asia.
The challenge in maintaining operations is exacerbated by restrictions on labor mobility, given quarantine orders and curtailment of cross-border movements by governments to reduce the risk of imported infections.
Beyond the impact felt on the supply side, consumer demand is fluctuating unevenly across different product categories. General consumer spending is contracting due to fears of economic instability, shifts in consumer patterns as more people stay home, and sharp falls in tourist arrivals. According to Nikkei Asian Review, about 30 million Chinese travelers visit Southeast Asia in a year — the impact of travel restrictions on consumption is therefore considerable. Meanwhile, spending has spiked for certain consumer staples and health care products.
The situation is further complicated by daily developments, putting organisations under constant, extreme pressure.
Respond rapidly
In the short term, responsiveness and speed are vital. While it is crucial for supply chains to develop an effective response within the first two weeks of a disruption, organisations must beware of knee-jerk reactions that could jeopardize medium- and longer-term operability. Therefore, proper crisis management with accurate analysis and planning is key.
Mobilising a crisis task force for supply chains is crucial for quick identification and quantification of critical components and existing gaps to reveal production constraints. At the same time, organisations will need to reassess demand forecasts and transportation restrictions. These collective insights will serve as key inputs to adjust and optimize production plans and new operational requirements, helping to identify suitable alternative suppliers.
Beyond addressing these operational risks, the task force will also need to seek greater visibility over many other business risks. This includes assessing whether at-risk suppliers may invoke force majeure clauses and their contractual obligations, as well as identifying cash flow constraints.
Tracking World Health organisation data and global travel restrictions and policies overlaid with the organisation’s supply chain enables businesses to identify current risks and anticipate future ones. Such risk factors and information can be incorporated into strategy planning and business simulation exercises, such as war-gaming, to plan for a range of scenarios — which is particularly important for a crisis that is constantly evolving.
As supply chains respond rapidly to mitigate immediate risks, organisations need to avoid short-termism in their decision-making. Given that COVID-19 is expected to fundamentally remap global supply chains, today’s decisions could impact their future resiliency.
Build resiliency
While most organisations recognize the importance of building supply chain resiliency, the current crisis reveals that it has not been an organisational priority. For far too long, supply chains have been focusing largely on cost optimization and operational efficiency instead of planning for demand changes and strategising on different potential scenarios.
organisations keen to boost their resiliency will need to apply the analytical approach used to identify critical gaps in the short term and conduct a more comprehensive end-to-end supply chain risk assessment. This assessment should include direct suppliers, intermediaries and raw material suppliers. They would then need to stress test the supply chain, identify critical risk scenarios and define potential responses.
To demonstrate that this is more than a paper exercise, organisations will need to follow through by taking remedial actions to mitigate weak spots and invest in capabilities in-house to build and manage supply chain resilience. Creating network flexibility through investments in single- or multi-site production, or through fully owned or contract manufacturing, can help to mitigate lengthy setup times and manage the costs of alternative sourcing.
Manufacturers in Southeast Asia are currently struggling to manage these challenges. For example, The Straits Times reported that the garment industry across the region is running out of woven fabric mainly sourced from China, while facing a fall in orders. As a result, some 60 factories in Cambodia had stopped operating and more than 18,000 workers had been temporarily laid off, according to the country’s prime minister in March. Such situations drive home the importance of scenario planning, which can be aided by emerging technologies, such as digital twin technology that creates a virtual replica of supply chains for organisations to stress test.
A supply chain with these capability build-outs, coupled with robust risk intelligence monitoring, or what supply chains call control towers, would enable organisations to develop the required rapid response in the next crisis. To be alerted on abnormalities as early as possible, organisations will need to invest in risk monitoring and advanced analytics reporting tools, as well as an early warning system to monitor incidents. Also needed is an alternative plan covering operating procedures and responses that will be triggered by disruptions, such as external and internal communication protocols, mobilization of key teams and delegation of authority.
Many organisations may wish that they could turn back the clock to build in resiliency in their supply chains ahead of COVID-19. To be better prepared for what lies ahead, organisations will need to stop delaying and start building resiliency in their supply chains today. This requires development of a rapid response to manage immediate supply chain disruptions, while assessing and plugging the longer-term gaps.
The author is EY Global Procurement Capability Leader, Partner, Advisory Services – Supply Chain and Operations, Ernst & Young Advisory Pte. Ltd. The views reflected in this article are the views of the author and do not necessarily reflect the views of the global EY organisation or its member firms.